След внутреннее напряжение

Перенастроите зарядное устройство. Если ошибка сохранилась, устройство, вероятно, неисправно. Рисунок 9 — Несплавление.
Физическая сущность пережога состоит в том, что кислород из окружающей атмосферы при высокой температуре проникает в глубь нагреваемого металла и окисляет границы зерен. В результате окисления границ зерен механическая связь между зернами ослабевает, металл теряет пластичность и становится хрупким, что при последующей обработке может привести к образованию трещин.
Дефекты при закалке. В процессе нагрева под закалку и при закалке могут появляться следующие дефекты: трещины, деформация и коробление, обезуглероживание, мягкие пятна. Закалочные трещины - это неисправимый брак, образующийся в процессе термической обработки. Они являются следствием возникновения больших внутренних напряжений.
Трещины возникают при неправильном нагреве перегреве и большой скорости охлаждения в деталях, конструкция которых имеет резкие переходы поверхностей, грубые риски, оставшиеся после механической обработки, острые углы, тонкие стенки и т д. Закалочные трещины, обычно расположенные в углах деталей или инструмента, имеют дугообразный или извилистый вид.
Деформация и коробление деталей происходят в результате неравномерных структурных и связанных с ними объемных превращений, обусловливающих возникновение внутренних напряжений в металле при нагреве и охлаждении. Мягкие пятна - это участки на поверхности детали или инструмента с пониженной твердостью. Такие дефекты образуются при закалке в процессе охлаждения в закалочной среде, когда на поверхности детали имелась окалина, следы загрязнений и участки с обезуглероженной поверхностью.
Дефекты сварки плавлением. Дефект сварного соединения в виде локального разрыва металла по границам кристаллизующихся зерен или по самим кристаллам металла - рисунок 2. Дефект виден невооруженным глазом или через лупу небольшого увеличения до 20 крат при визуальном контроле. Трещины могут возникать как в основном металле конструкции, так и в зоне сварного шва.
При сварке различают горячие и холодные трещины. Горячие - хрупкое межкристаллитное разрушение в процессе кристаллизации сварного шва; холодные — хрупкое межзеренное разрушение свежезакаленного сварного соединения под действием остаточных сварочных напряжений, которые происходят в течение 1, 2-ух суток после окончания сварки. Горячие трещины возникают вследствие загрязненности свариваемого и присадочного металла серой и фосфором, а также при грубых нарушениях технологических режимов сварки излишние тепловложения, быстрая скорость охлаждения.
Холодные трещины возникают в среднелегированных и высоколегированных сталях перлитного и мартенситного классов при значительной концентрации диффузионного водорода в зоне сварки и наличии растягивающих напряжений. Холодные трещины имеют светлый блестящий излом без следов высокотемпературного окисления, горячие представляют собой извилистый окисленный разрыв металла.
Располагаться трещины могут как на поверхности наплавленного металла, так и на поверхности основного металла в зоне термического влияния с ориентацией вдоль или поперек сварного шва. Также трещины могут встречаться в кратере — углублении в центре сварного шва, возникающем вследствие усадки расплавленного металла при резком обрыве дуги при прерывании процесса сварки. Дефект сварного шва в виде полости округлой формы, заполненной газом. На рисунке 3 наглядно представлена полость произвольной формы, без углов, образованная газами, задержанными в расплавленном металле.
Внешние признаки дефекта отсутствуют, так как он находится внутри сварного шва. В сварочной ванне образуются пузырьки водорода, азота, окиси углерода и др. Эти пузырьки фиксируются в металле шва при его кристаллизации. Трубчатая полость в металле сварного шва из-за выделений газа. Форма и положение свища зависят от режима затвердевания и вида газа. Обычно свищи скапливаются и распределяются «елочкой», рассмотрим на рисунке 4. Внешние признаки отсутствуют, так как дефект находится внутри сварного шва.

Обнаруживают методом неразрушающего контроля. При сварке угловых швов в различных пространственных положениях, отличных от нижнего, подъемная сила не может выдавить пору наружу. Поверхностная пора. Дефект, нарушающий сплошность поверхности сварного шва видимый невооруженным глазом или через лупу небольшого увеличения 2 — 4-х при визуальном контроле.
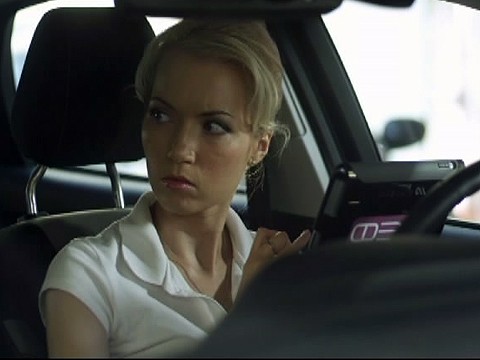
Из-за высокой вязкости шлака на поверхности сварочной ванны и высокой скорости затвердевания шлака газовый пузырек это могут быть пузырьки водорода, азота, водяного пара и окиси углерода, основные возбудители пор при сварке сталей — водород и азот не может всплыть пройти через уже затвердевшую шлаковую корку и кристаллизуется в виде полости на поверхности сварного шва.
Газовая пора, нарушающая сплошность поверхности сварного шва изображена на рисунке 5. Причины возникновения — повышенная вязкость шлака, расположенного на поверхности жидкой сварочной ванны.
Усадочная раковина. Полость, образующаяся вследствие усадки металла во время затвердевания. Дефект виден невооруженным глазом или через лупу небольшого 2—4-х увеличения при визуальном контроле. Под действием дуги зеркало сварочной ванны деформируется, приобретая вогнутый вид. При внезапном обрыве дуги оно не успевает спрямиться и затвердевает в форме впадины, что можно рассмотреть на рисунке 6.
Твердое включение. Твердые инородные вещества металлического или неметаллического происхождения в металле сварного шва. Включения, имеющие хотя бы один острый угол, называются «остроугольными». Тугоплавкие частицы инородных металлов и других включений вольфрам, медь, корунд, кварц и т.
Шлаковое включение. Дефект в виде вкрапления шлака в сварном шве рассмотрен на рисунке 8. В разных условиях образования включения бывают линейные 1 на рисунке 8 ; отдельные 2 на рисунке 8 ; кучно расположенные - скопления 3 на рисунке 8.
Гранулы флюса, обмазка электродов, шихта порошковой проволоки не успев вступить в реакцию с расплавленным металлом и всплыть на поверхность жидкой сварочной ванны, быстро кристаллизуются в ней. Отсутствие соединения между металлом сварного шва и основным металлом или между отдельными валиками сварного шва. На рисунке 9 различают несплавления: по боковой стороне 1 на рисунке 9 , между валиками 2 на рисунке 9 , в корне шва 3 на рисунке 9. Внешние признаки: отсутствуют, так как дефект находится внутри сварного шва.
При дуговой сварке дуга не расплавила часть кромки стыка и не сформировала шов с ее участием. Дефект в виде несплавления в сварном соединении вследствие неполного расплавления кромок или поверхностей ранее выполненных валиков сварного шва Бывает в корне или в сечении шва, показано на рисунке Сварочная дуга не может расплавить нижнюю кромку разделки и сформировать шов с её участием. Расплавленный металл не проникает к корню соединения. Дефект в виде углубления по линии сплавления сварного шва с основным металлом.
На рисунке 11 продольное углубление на наружной поверхности валика сварного шва. Жидкий металл сварочной ванны вытесняется в ее центральную часть. Высокая скорость кристаллизации и низкая смачиваемость препятствуют растеканию металла в границах расплавления. Дефект в виде натекания металла шва на поверхность основного металла или ранее выполненного валика без сплавления с ним.
Избыток наплавленного металла сварного шва, натекший на поверхность основного металла, но не сплавленный с ним, показан на рисунке Внешние признаки: избыток металла шва по его краю. Дефект виден невооруженным глазом при визуальном контроле. При формировании шва избыток металла сварочной ванны натекает на холодные кромки основного металла, не образуя с ним соединения. Дефект в виде вытекание металла сварочной ванны, в результате чего образуется сквозное отверстие в сварном шве, показан на рисунке Внешние признаки: сквозные отверстия или полости, образованные вследствие расплава сварочной ванны.
В сварочной ванне образуется чрезмерный объем жидкого металла. Он не удерживается силами поверхностного натяжения и самопроизвольно вытекает из шва.
Эксплуатационные дефекты. Эксплуатационные дефекты возникают в процессе эксплуатации трубопроводов. К ним относятся коррозионные повреждения на внутренней и наружной поверхностях трубопровода, плотные отложения.
Для трубопроводов, транспортирующих сероводородсодержащие среды, кроме язвенной коррозии, характерны водородные расслоения и сероводородное растрескивание металла.
Водородные расслоения рисунок 14 возникают при длительной эксплуатации трубопроводов в области металлургических дефектов металла труб, причем этот процесс протекает интенсивнее на участках трубопроводов с застойными зонами или в металле трубопроводов, находящихся в консервации. Основные водородные расслоения возникают в области ликвационных зон и состоят из нескольких соединившихся между собой макрорасслоений, являющихся результатом объединения межкристаллитных микрорасслоений.
Почвенная коррозия. Подземные трубопроводы могут корродировать и под влиянием работы микрогальванических пар, появляющихся по всей длине трубопровода вследствие его неодинакового состава или различной аэрации почвы на соседних участках. Почвенная коррозия металла труб в местах их контакта с наиболее коррозионно-активным верхним слоем может привести к образованию коррозионных повреждений значительной глубины рисунок Язвенная коррозия характеризуется появлением на поверхности конструкции отдельных или множественных повреждений, глубина и поперечные размеры которых от долей миллиметра до нескольких миллиметров соизмеримы рисунок 16а.
Язвенная коррозия обычно сопровождается, образованием толстых слоев продуктов коррозии, покрывающих всю поверхность металла или значительные ее участки вокруг отдельных крупных язв характерно для коррозии незащищенных стальных конструкций в грунтах. Язвенная коррозия труб со временем переходит в сквозную рисунок 16а. Язвы являются острыми концентраторами напряжений и могут оказаться инициаторами зарождения усталостных трещин и хрупких разрушений.
Для оценки скорости язвенной коррозии и прогнозирования ее развития в последующий период определяют средние скорости проникновения коррозии в наиболее глубоких язвах и количество язв на единицу поверхности. Эти данные в дальнейшем используют при расчете остаточного срока эксплуатации оборудования и трубопроводов. Коррозионное растрескивание — вид квазихрупкого разрушения металлов и сплавов при одновременном воздействии статических напряжений растяжения и агрессивных сред; характеризуется образованием единичных и множественных трещин, связанных с концентрацией основных рабочих и внутренних напряжений.
Трещины могут распространяться между кристаллами или по телу зерен, но с большей скоростью в плоскости, нормальной к действующим напряжениям, чем в плоскости поверхности.
КРН магистральных газопроводов — разрушение металла труб в результате длительного и одновременного воздействия на их наружную поверхность механических напряжений, достигших порогового значения, и грунтового электролита.
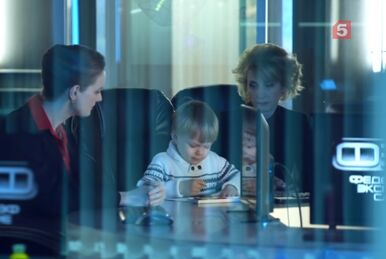
Необходимым условием развития стресс-коррозионных трещин является доставка коррозионно-активной среды в вершину развивающейся трещины при сохранении высокого уровня напряжений. Коррозионное растрескивание под напряжением проявлялось на трубах магистральных газопроводов в основном диаметрами , и мм с пленочным антикоррозионным покрытием холодного нанесения.
Преимущественно в нижней половине сечения трубы под отслоившейся изоляцией образовывались колонии одинаково направленных в большинстве случаев параллельно оси трубы поверхностных трещин различных размеров рисунок Для труб магистральных газопроводов стресс-коррозия, по-видимому, связана с исходным состоянием труб — уровнем и характером распределения остаточных напряжений технологического или конструктивного происхождения и неоднородностью поверхности металла, например, с наличием поверхностных строчечных неметаллических включений размером более третьего номера.
Характерным признаком КРН является множественный характер зарождения трещин, образующих стресс-коррозионный дефект «поле или колония трещин» , и их предпочтительная ориентация относительно растягивающих напряжений.
Усталостные трещины. При нагружении зарождение трещин в металле труб связано с возникновением больших растягивающих напряжений в результате скопления дислокаций, образующихся у препятствий или расположенных вдоль полос скольжения, коагуляции вакансий, возникновения экструзий выдавливание тонких лепестков металла и интрузий провалы на поверхности металла. Период распространения усталостной трещины включает четыре этапа: кристаллографического роста I, стабильного роста II, нестабильного роста III и статического долома окончательного разрушения IV.
Усталостные повреждения наиболее заметно протекают в зонах концентрации напряжений. Неразрушающий контроль Статьи. Содержание Введение 1. Дефекты стальных слитк ов 1.
Дефекты проката и труб 1. Дефекты термической обработки 1. Дефекты сварки плавлением 1. Эксплуатационные дефекты Видео лекция Маслова Б. Основные дефекты сварных соединений и их выявляемость методами НК. Дефект в виде несплавления в сварном соединении вследствие неполного расплавления кромок или поверхностей ранее выполненных валиков сварного шва.
Рисунок Язвенная коррозия: а — начало зарождения язв, б — окончательная стадия разрушения. Трещины КРН на поверхности: а — основного металла трубы, б — вблизи продольного сварного шва.
Информация об источнике Диагностирование объектов нефтегазовой промышленности. Читайте еще по теме. Версия для печати. Инновационный шаблон специалиста НК для измерения параметров отклонений и дефектов сварных соединений различных типов ВИК не для галочки!
Рисунок 2 — Виды трещин. Рисунок 3 — Пора. Рисунок 4 — Свищ. Рисунок 5 — Поверхностная пора. Рисунок 6 — Усадочная раковина. Рисунок 7 — Твердое включение. Рисунок 8 — Шлаковое включение.
Рисунок 9 — Несплавление. Кроме того, как правило, увеличивается трудоемкость изготовления самих изделий.
Деталь должна быть спроектирована так, чтобы после формования не требовалась или была бы минимальной дополнительная механическая обработка снятие облоя. Стенки изделия. Литьевые детали целесообразно конструировать минимальной толщины, обеспечивающей необходимые механические свойства при хорошем заполнении литьевой формы. Это приводит к меньшему расходу материала при более высокой производительности вследствие меньшей продолжительности охлаждения детали в форме. Технологические уклоны.
Для обеспечения свободного извлечения отливки из формы на внешней и внутренней поверхности изделия, ребрах, отверстиях необходимо предусматривать технологические уклоны. Уклоны внутренних поверхностей и отверстий должны быть больше уклонов наружных поверхностей, так как при раскрытии формы внутренние поверхности за счет усадки обжимают оформляющие элементы, а наружные, наоборот, отходят от стенок формы и меньше препятствуют удалению отливки.
Отверстия в литьевых деталях. Специальные отверстия создаются с помощью оформляющего знака, который находится в полости литьевой формы. Отверстия, получаемые в процессе формования, в отличие от получаемых механической обработкой, могут иметь самую разнообразную и сложную форму сечения.
Можно получать отверстия со взаимно пересекающимися под различными углами осями, однако это резко усложняет конструкцию формы и повышает стоимость изделия. Большинство изделий из пластмасс имеют наружную, внутреннюю или и ту, и другую резьбу, которую получают как в процессе формования, так и нарезанием механическим способом.
Возможность непосредственного получения резьбы в процессе формования, несмотря на усложнение конструкции формы, дает значительные преимущества, так как исключает операции механической обработки. Приливы, выступы.
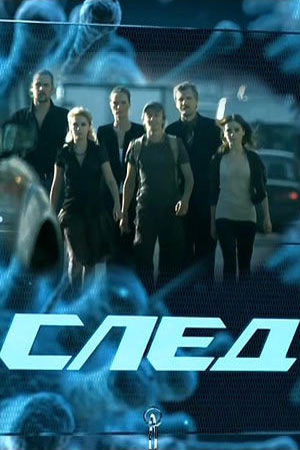
Конструкция пластмассового изделия по возможности не должна иметь значительных выступов или приливов. К технологическим выступам относят выступы, предназначенные для размещения выталкивателей. Они могут отсутствовать на достаточно прочных изделиях, но желательны на тонкостенных.
Для увеличения прочности пластмассового изделия, повышения износостойкости, обеспечения специальных свойств электрическая, магнитная проводимость , улучшения декоративных свойств в конструкцию изделия допускается вводить металлическую или другую арматуру керамическую, стеклянную, пластмассовую другого вида, резиновую и др.
Накатка, рифления, надписи. Накатку и рифления на изделиях из пластмасс следует выполнять прямыми ребрами, параллельными направлению выталкивания изделия из формы. Наиболее технологичным рельефом является полукруглый профиль. Надписи буквы, цифры, знаки на изделиях обычно получают в процессе формования, причем на поверхностях, параллельных плоскости разъема формы.
Конструкция изделия должна предусматривать место подвода литника, положение выталкивателей, следов от вставок и расположение линии разъема формообразующих элементов. Расположение впускного литникового канала влияет на характер течения расплава в форме, на внутренние напряжения, образование спаев в изделии, следы течения на поверхности изделия, на усадку, деформацию изделия при высоких температурах, прочность изделия.
Внутреннее напряжение обычно наиболее значительны в области впуска, поэтому место впуска в изделии наиболее опасно и подвержено растрескиванию или разрушению. Расположение линий спаев зависит от местонахождения впуска, толщины и сложности конфигурации детали.